
METAL FORMING SIMULATION TECHNOLOGY
Developing or modifying a metal forming process can involve significant tooling and capital cost. Finite element simulation technology reduces the financial risk of innovation by creating quantitative, in-depth studies of processes like hot, warm, and cold forming, trimming, shearing, rolling, bending and drawing. These studies then can be used to identify the best path forward.
We use DEFORM™ finite element simulation software to create a custom computer model of your existing or proposed process. Using this model, we explore how parameters and design choices affect material flow, tool load, stress, and defect formation. Armed with this knowledge, we help you move forward with confidence to address the challenges your business faces today and tomorrow.

THE FREEDOM TO INNOVATE
DEFORM™ finite element simulations empower designers and engineers with the inside information they need to bring innovative designs to market faster and with less risk.
The ability to show how a process functions can pave the way to improved understanding, smoother projects, and happier customers. Simulation animations can be a significant asset when training your production staff to produce a new part or troubleshoot an existing process. They also can be used as a sales and marketing asset when talking with customers.
Hammer Forging
Ring Rolling
Ring Rolling view 3
Thread Rolling
Billet Heatup
Thermal Expansion
Thermal Expansion 2
Furnace Operation view 1
Furnace Operation view 2
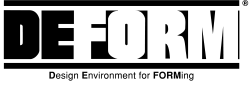
The applications are endless
Visit Scientific Forming Technologies, the creator of DEFORM™ finite element simulation software, to view videos of additional applications.